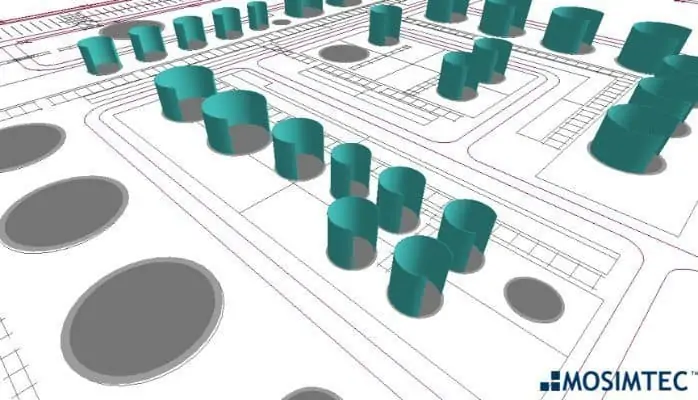
MOSIMTEC has recently completed simulation models for clients in crude oil and refined products storage and transportation logistics. We wanted to share how our virtual tools (more accurately described as precision instruments) helped our clients bring clarity to their complex operations.
Some of our recent accomplishments included simulating:
- the world’s largest petrochemical facility,
- one of North America’s largest crude-by-rail loading facility,
- North America’s most complex condensate transportation system, and
- one of North America’s largest refinery supply chain operations.
MOSIMTEC has proven returns on their investment in our simulation models to be more than 10-fold. This is not surprising as the cost for materials and labour is significantly higher in the crude oil business compared to any other industry. Time to market is critical in the oil industry. When oil was ~$100/bbl a price war was raging in terms of acquiring the proper materials to construct their operations as well as skilled personnel to run their operations. This created a perfect storm where costs in both labour and materials skyrocketed.
By combining our simulation models with our crude oil storage and transportation expertise we have created models that allowed our clients to experiment with multiple options to find what is the best solution for their needs. Various aspects were brought to the table and all stakeholders say was equally evaluated to find the right solution and the best opportunity. Aspects we modeled included but are not limited to:
- Blending of crudes in a tank as well as a pipeline taking into account density and sulphur concentrations.
- Shrinkage of multiple crude types continuously blending within a tank and a pipeline.
- Optimal tank utilization for blending and/or batch scheduling.
- Manpower requirements and optimal staging for crude-by-rail operations.
- Nominations and scheduling optimization for multiple pipelines with various flow rates and batch sizes while sharing one meter bank.
The model will continuously apply the blending and shrinkage algorithms based on a predetermined mass balance value. For example, one model we created was to measure a monthly nomination of 4.5 million barrels of 10 different crude types into a multiple tanks it made over 17,000 calculations when applying our our blending and shrinkage algorithms. The data this generated allowed our client to understand what their limitations were in accepting more crude and which type could they reasonably accept while remaining within the constituents of the crude classification.
The model simulation approach will make a spreadsheet obsolete.
There are many different approaches we have applied our expertise within our client’s companies as each department has their own agenda. In one case our models helped bridge the gap of understanding between the business development department with their goals to the maximize the opportunity to generate revenue and connecting to the engineering department with the physical limitations of expanding the assets. By building a simulation model of the existing asset it allowed us to experiment with adding additional services and seeing if they were economical as well as physically capable within the constraints inherent in the facility design.
Please contact us if you would like to learn more about our oil & gas simulation modeling for petroleum storage and transportation.