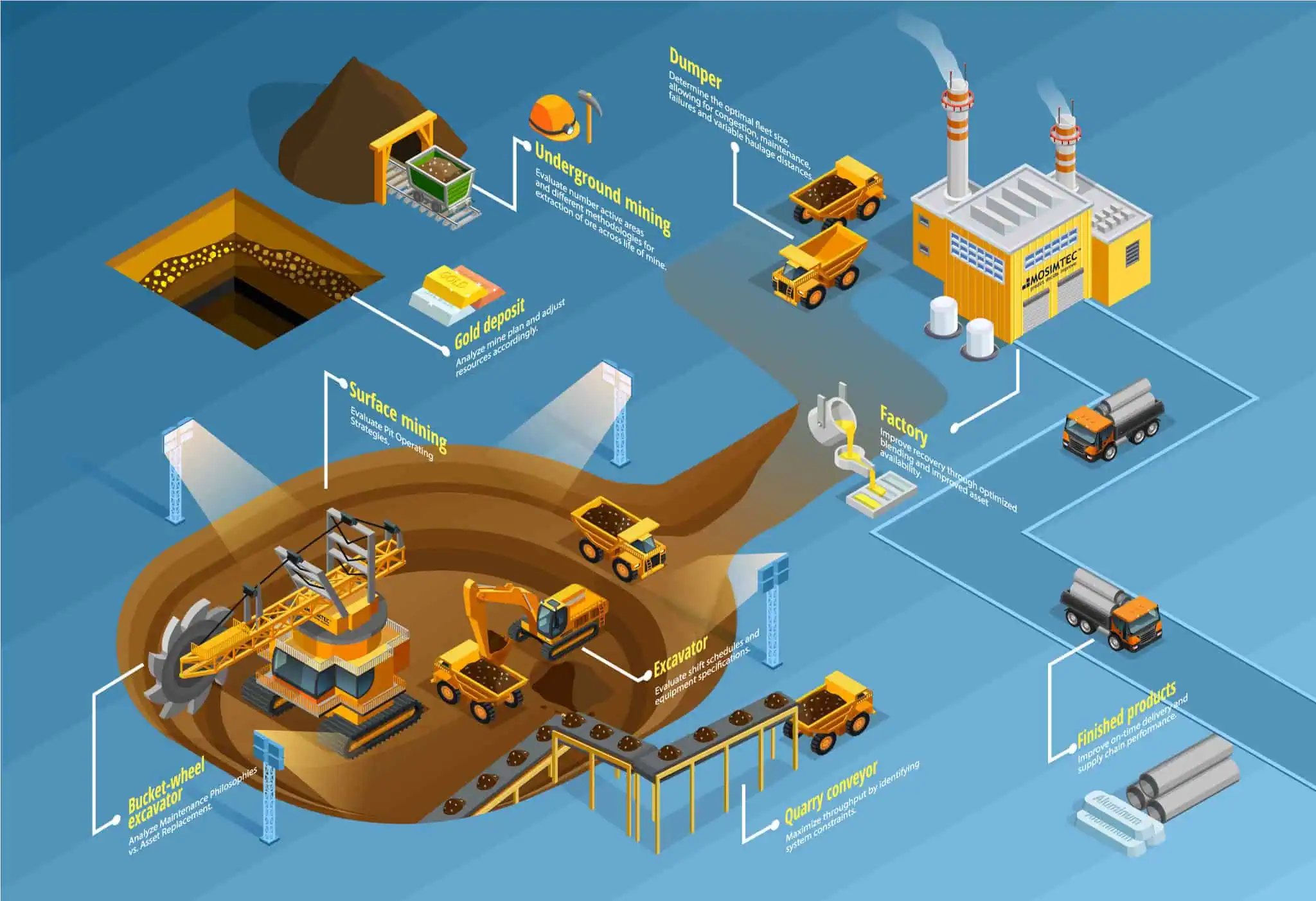
MOSIMTEC supported Sibanye-Stillwater (SS) at their Nye Mine. SS produces platinum, palladium and gold. The Nye Mine in MT is ~4 miles long and 4500 feet from top to bottom. MOSIMTEC developed a virtual underground mine using a dynamic simulation model/digital twin.
Rock is mined in rounds which are 14’ feet x 10’ wide openings, advance 9 feet at a time along the ore body. The broken rock is removed from the heading and enters the muck-hall system enroute to the surface/mill complex. The mill grinds the rock to extract the ore and concentrate is shipped to the metallurgical complex for refining. Leftover rock from the mill is routed to the backfill system. When a heading has all ore removed, it is filled with paste (cement mixed with rock), sand or CRF (unprocessed waste rock mixed with cement). Backfill allows mining to proceed up/down the ore body.
One area modeled was the muck-haul system. There are 4 ways that muck can be transported – trucks, passes (vertical holes between levels), trains and hoists. Muck is handed off from one form of transport to another, over and over, until the rock reaches the surface/mill. The actual route of rock from a heading to the surface can be very complex.
The backfill system is also complex. The mill is the only source of tails for the backfill system. The tails flow into the paste plant or to one of two transfer points. These points serve one of five sand plants, which each serve different areas of the mine. This means that backfill flow to any one area is dependent on mill throughput, also demand in other mine areas.
Primary project focus was to (1) understand interdependence between mining, backfill and logistics (2) understand ability of backfill plant to keep up with the mining schedule and identify when/where bottlenecks occur and (3) estimate mobile equipment/transport fleet requirements to meet mine plan throughput targets.
The process digital twin of the backfill operation provided multiple benefits. Regular planning/scheduling of backfill that used to take 2-3 hours/week was cut to 20 minutes. When changes occur to the mining schedule, re-planning can be done much more easily. Bottlenecks/sequencing issues can be discovered months in advance versus current visibility of 6 weeks. Long-term mine planning for activities 2-30 years out, typically done annually, can now be done quarterly, allowing the team to true up their long-term forecasts. Planning/scheduling of backfill can be done without detailed knowledge of mining systems, cutting the learning curve for new hires.
MOSIMTEC provides dynamic simulation of the mining process. We have done many mining projects including all aspects of the value chain (mining, processing, supply chain, more) across many mine types/methods, geographies and minerals/products over 15 years to help companies improve performance. We can help future-proof your mining operation.
#mining #digital twin #refining #supplychain #virtualmine
Read More: https://mosimtec.com/sibanye-stillwater-backfill-sim/